Case Study: Transforming Electrical Infrastructure for Innova NanoJet’s Expansion Project
Client: Innova NanoJet
Industry: Medical Appliance Manufacturing
Location: Vale of Leven Industrial Estate
Project Duration: 2 months
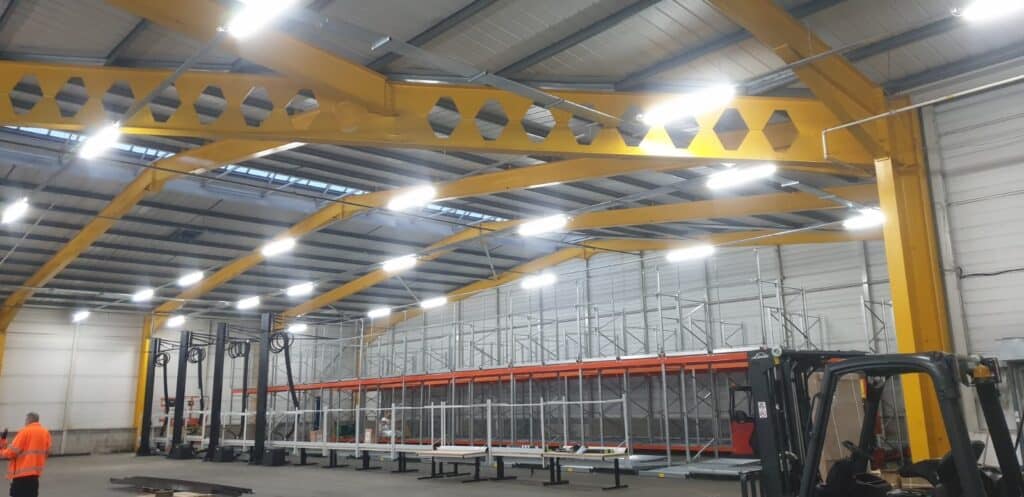
Project phases
Client Design Meetings, Electrical Drawing Phase, Striping Out Phase, Main Containment Phase, Main Wiring Phase, Testing Phase
Project background
Innova NanoJet, a innovative medical appliance manufacturer that are making life altering appliances, partnered with Wilson Electrical for a pivotal expansion project.
The initiative aimed not only to bolster production capabilities to a level never seen before at the job site in Dumbarton but also to facilitate the installation of cutting-edge manufacturing equipment, including CNC machines, injection moulding units, CMM Machines, compressors, and 3-phase vacuum lifters.
The factory itself will at full operating capacity will be home to over 100 staff members and an intended production rate of 10 million units per year.
Project phases
Client design meetings
Wilson Electrical, collaborating closely with Innova NanoJet’s stakeholders, initiated the project with comprehensive client design meetings.
Engaging key personnel allowed our team to grasp specific electrical needs, equipment specifications, and future growth plans. Iterative discussions ensured the final design aligned seamlessly with Innova NanoJet’s vision.
Challenges:
Balancing diverse departmental requirements which include a robust 8 week schedule.
Aligning client expectations with technical feasibility in relation to output while upholding the highest standards.
Solutions:
Regular feedback sessions in person, online meetings and design revisions.
Detailed presentations to clarify technical aspects, whilst simultaneously working with machine manufacturers.
Electrical drawing phase
Wilson Electrical delved into the meticulous creation of electrical drawings post-design meetings.
These schematics served as the blueprint for the entire infrastructure, addressing power distribution, equipment connections, safety features, and scalability considerations.
Multiple reviews and changes with Innova NanoJet’s head engineering team ensured accuracy and alignment with their expectations.
Challenges:
Balancing technical requirements with user-friendly design.
Incorporating scalability features for expansion that met the clients own future projections.
Solutions:
Utilizing CAD for precision and for all staff members to work to a minute detail.
Changing and amending to suit operational limitations.
Strip-out phase
The strip-out phase marked the beginning of physical changes to the existing electrical systems. Wilson Electrical ensured careful planning and coordination to minimize downtime.
Dismantling existing components in a step by step process to ensure partial functionality for day to day running of the factory and to provide temporary lighting and power.
Challenges:
Minimizing production downtime during the strip-out phase.
Adapting to unforeseen challenges in the existing infrastructure.
Solutions:
Conducting the strip-out phase in stages to maintain partial functionality.
Agile problem-solving and quick adjustments to overcome challenges on a weekly basis working with the manufactures often vague requirements.
Containment phase
The containment phase involved the installation of conduits, cable trays, and other structures.
Beyond technical specifications, Wilson Electrical prioritized safety, cost considerations and compliance beyond industry standards.
The design accommodated present needs and considered future expansions and maintenance requirements with an allowance for larger cable trays to provide a platform for easier additions to fall in line with Innova Nanojet’s projections.
Challenges:
Navigating the complex layout within a short time frame.
Ensuring compatibility with existing structures and equipment while complying with technical specifications.
Solutions:
Collaborating with facility managers to optimise the layout.
Customising containment solutions for seamless integration.
Wiring phase
With enhanced drawling lead containment structures in place, the wiring phase began.
Wilson Electrical’s skilled electricians connected power sources and integrated control systems and established a robust network for diverse manufacturing equipment and an entirely new lighting layout to suit factory floor realignment.
Coordination with equipment manufacturers ensured compatibility and seamless integration.
Challenges:
Coordinating with multiple equipment manufacturers from a range of countries.
Ensuring precision and accuracy in wiring to prevent issues during testing.
Solutions:
Regular communication and collaboration with equipment manufacturers.
Employing skilled electricians with expertise in diverse equipment integration.
Regular site meetings to respond fast to changes.
Testing phase
Rigorous testing followed the completion of the wiring phase. This included comprehensive checks of power distribution, equipment functionality, safety systems, and emergency shutdown procedures.
Collaborative efforts with equipment manufacturers ensured each component operated at peak efficiency with the temporary power supplies (generator) and the incoming upgraded power supply coming into the facility.
Challenges:
Coordinating the testing schedule with Innova NanoJet’s production requirements.
Solutions:
Thorough pre-testing to identify and address issues.
Developing a flexible testing schedule to minimize disruption to production.
Multiple of our employees are 2391 qualified to react to any testing needs.
Key collaborations
Throughout the project, Wilson Electrical collaborated closely with manufacturers of CNC machines, injection moulding units, compressors, and 3-phase vacuum lifters.
This approach facilitated seamless integration, with the team adapting electrical solutions to meet the unique requirements of each manufacturing process.
Team and future plans
The Wilson Electrical team, consisting of eight dedicated staff members for this specific project, played a pivotal role in the successful execution of the project.
Their expertise and collaborative spirit contributed to the timely completion and success of the electrical infrastructure upgrade, with a happy client keen to continue new and planned works in 2024.
Additionally, there are exciting prospects on the horizon. Phase 2 of the project is scheduled for 2024, reflecting Innova NanoJet’s commitment to continued growth and innovation.
Wilson Electrical looks forward to leveraging its experience and expertise to contribute to the success of this next phase. This, among other projects, is an exciting start to 2024 and the continued growth of both businesses.
Results and achievements
Timely project completion: The project was completed within the stipulated 2-month timeframe despite multiple welcome additions, minimizing disruptions to Innova NanoJet’s production schedule.
Enhanced manufacturing capabilities: The upgraded electrical infrastructure successfully powered advanced high-end CNC machines, CMM, injection moulding units, compressors, and 3-phase vacuum lifters and 16 workbenches, enhancing Innova NanoJet’s manufacturing and rigorous product testing capabilities.
Conclusion
The collaborative efforts between Innova NanoJet and Wilson Electrical resulted in the successful execution of a complex and time-sensitive project.
The upgraded electrical infrastructure not only met the immediate needs of the medical appliance manufacturer but also provided a foundation for continued development, growth and innovation in the dynamic field of medical device manufacturing.
We look forward to Innova Nanojet being a long-term valued customer going forward.